Major equipment
I-PEX Precision Mold & Plastics (Shanghai) Co., Ltd. manufactures ultra-precision molds and automated equipment. We guarantee quality and ensure supply to the market by using various inspection equipment while mass-producing through automation of injection molding, pressing, plating, and assembly.
The following are the main facilities and functions of them that the company owns.
Manufacture of ultra-precision metal fittings and high-speed automation equipment
We started processing and manufacturing ultra-precision molds in 1991. We have a series of import processing equipment such as YASDA's ultra-high precision 5-axis machining center, Makino's precision 3-axis machining center, Mitsubishi's precision electric discharge machine and wire-cut electric discharge machine, Okamoto's precision forming grinding machine, Makino milling machine and IEPCO surface treatment equipment, as well as inspection equipment of Nikon and Mitutoyo. Manufacturing and assembling high-speed automation equipment for precision connectors and automotive parts began in 2011.
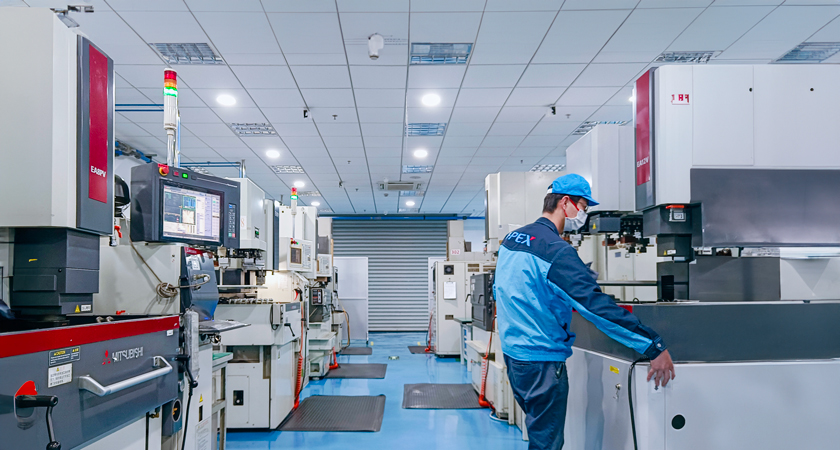
Injection molding
We started injection molding in 1992 and have thirty five general purpose injection molding machines (3T -180T).
We started insert molding processing in 2012, and have forty processing equipment.
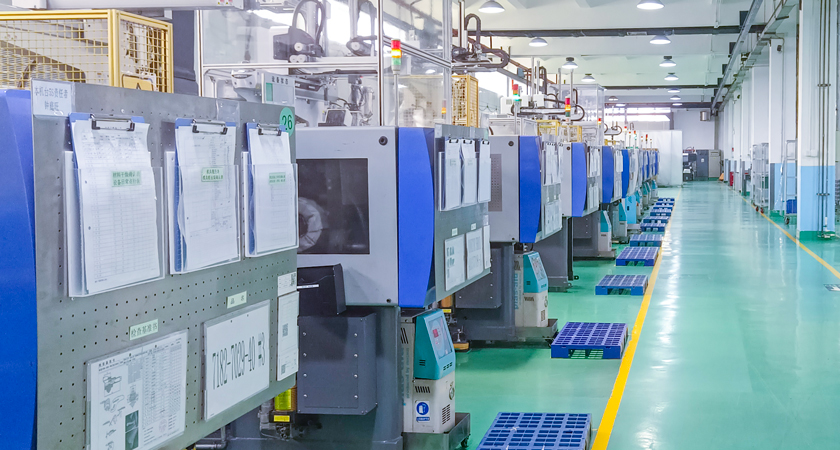
Stamping
We started press work in 2004, and currently own twenty one high-speed press machines including one 20T, eleven 30T and nine 40T.
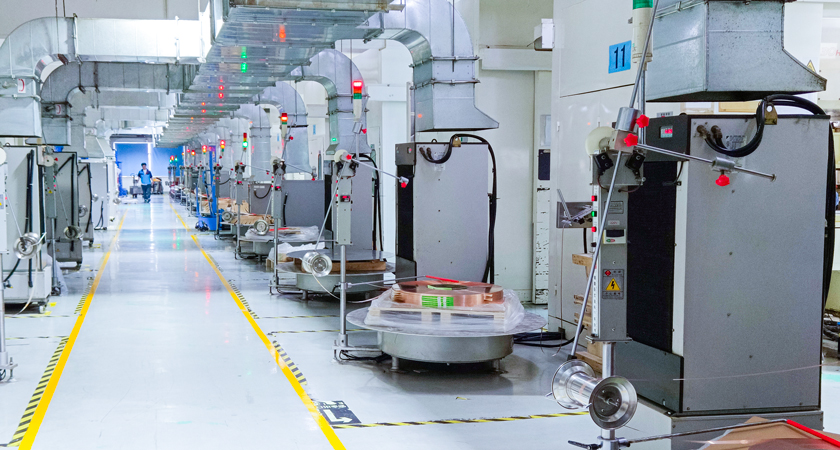
Plating
We began the plating process for mass production in 2007. We currently have a fully automatic plating line of reel-to-reel and are able to plate gold, nickel, tin copper-tin alloys and so on. Our technology makes is possible to handle products up to a height of 0.8 to 70 mm using several plating technologies such as precision plating with the plating film orientation, spraying plating, brush plating, and immersion plating.
The needs of high-end customers can be satisfied with our unique precision plating technology. This technology and the orientation of the plating film make it possible to plate a product of less than 1 mm on six plating areas with different coating thickness at the same time.
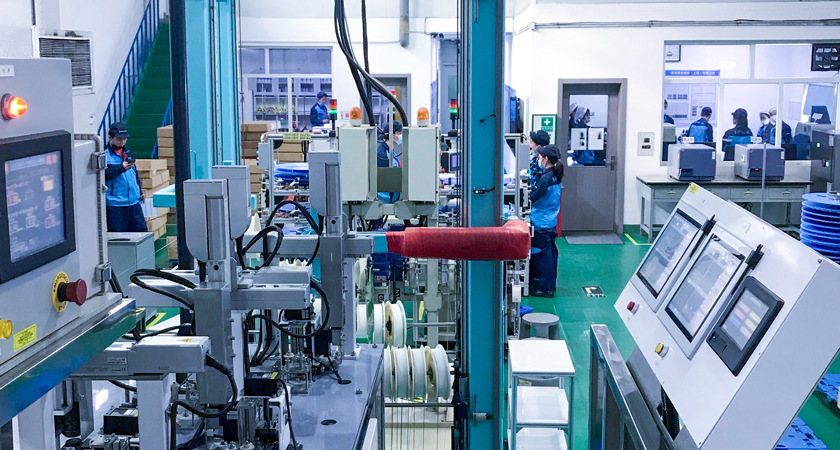
Automation of assembly
We began automation of connector assembly in 2011 (We own twenty six integrated equipment, including parts supply, assembly, electrical and image inspection, and sealing as well as twenty one automated equipment for image visual inspection.)
Automated assembly of automotive parts began in 2014.
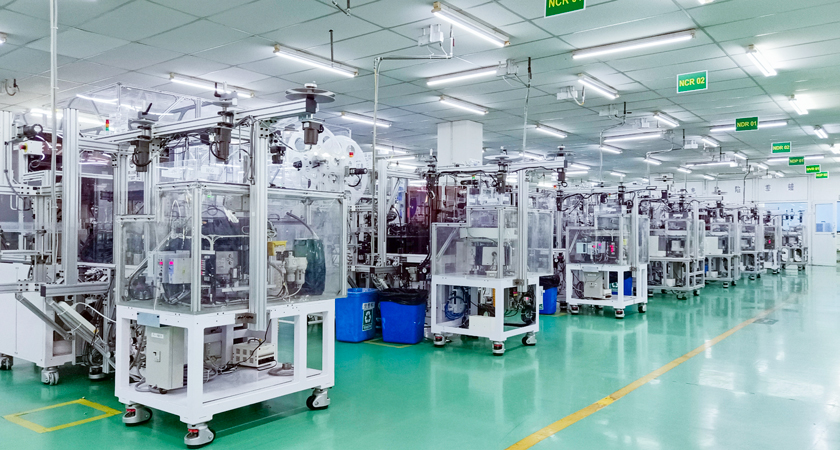
Quality Assurance证
In the Quality Assurance Division, we have equipment such as X-ray film thickness measuring instruments, solderability tester, constant temperature and humidity tester, heat resistance tester, salt spray tester, gloss meter, ICP analyzer, ultraviolet illumination meter, ED-XRF detector, tool microscopes, projectors, universal testing machines, non-contact 2.5-dimensional and contact 3-dimensional.
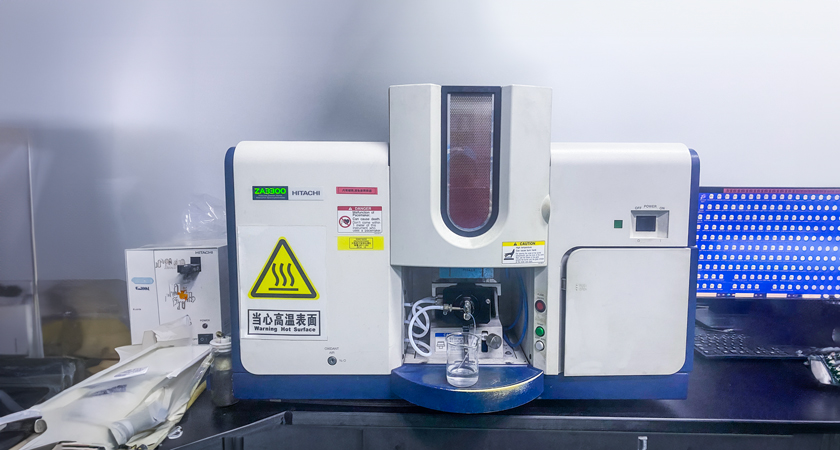