precision molding
1963 - 1972
From foundation to export of precision molds
Dai-ichi Seiko Co., Ltd. was established by founder Akira Konishi in Fushimi, Kyoto. With the module system for manufacturing molds that he invented himself, the company started out as a precision mold manufacturer with a venture spirit. In less than 10 years after its establishment, Dai-ichi Seiko’s advanced mold technology was highly evaluated internationally, and it won orders one after another from Japan and abroad. It built a solid business foundation as a precision mold manufacturer.
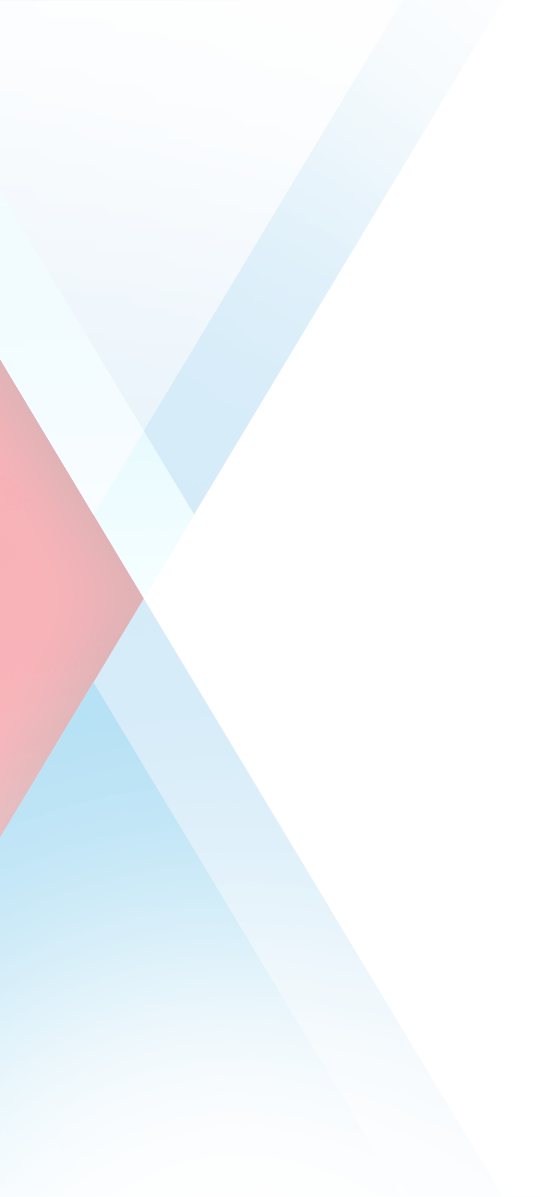
-
1960
The module system for manufacturing molds was invented, featuring a full-split structure, complete heat treatment hardening and complete machining.
1963
Establishment of Dai-ichi Seiko Co., Ltd.
In July 1963, at a time when Japan was striving for rapid economic growth, Dai-ichi Seiko Co., Ltd. was founded in Fushimi, Kyoto Prefecture, Japan. With the module system for manufacturing molds developed by founder Akira Konishi, the company got its start as a precision mold manufacturer that broke away from the handcrafting style of the traditional town factories. Molds manufactured using this module system featured (1) a split structure, (2) complete heat treatment hardening, and (3) complete machining. The advantages are as follows: (1) includes superior machinability and workability due to the ability to select appropriate materials and hardness for each area; (2) includes a dramatic increase in mold life and superiority in securing mirror surface quality; and (3) includes easy ultra-precision machining and stable dimensional accuracy and man-hours in production control.
The module system for manufacturing molds
-
Mold finished product
Photo of a set of mold parts using the modular system
-
Jig grinder 3SMO type work scene
-
-
-
-
1963
From craftsmanship to modern industry
Dai-ichi Seiko Co., Ltd. was established as a company specializing in the manufacture of high precision molds.
1963
Establishment of Dai-ichi Seiko Co., Ltd.
In July 1963, at a time when Japan was striving for rapid economic growth, Dai-ichi Seiko Co., Ltd. was founded in Fushimi, Kyoto Prefecture. With the module system for manufacturing molds developed by founder Akira Konishi, the company got its start as a precision mold manufacturer that broke away from the handcrafting style of the traditional town factories. Molds manufactured using this module system featured (1) a split structure, (2) complete heat treatment hardening, and (3) complete machining. The advantages are as follows: (1) includes superior machinability and workability due to the ability to select appropriate materials and hardness for each area; (2) includes a dramatic increase in mold life and superiority in securing mirror surface quality; and (3) includes easy ultra-precision machining and stable dimensional accuracy and man-hours in production control.
The module system for manufacturing molds
-
Mold finished product
Photo of a set of mold parts using the modular system
-
Jig grinder 3SMO type work scene
-
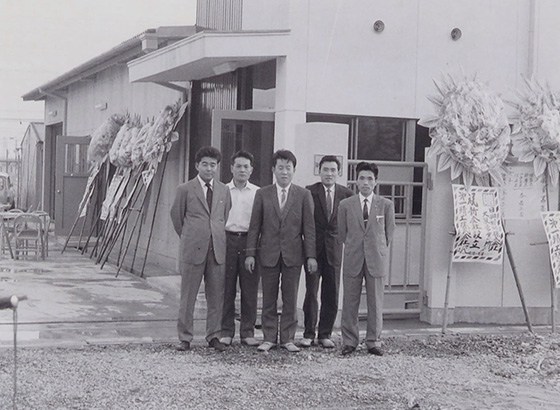
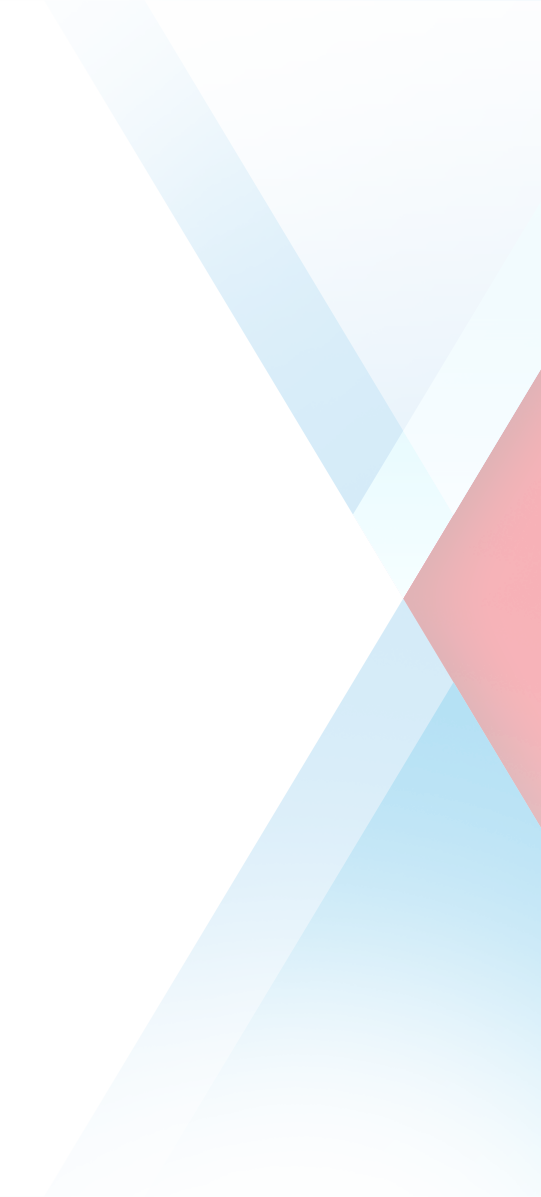
-
1964
Expanded the plant and established a jig department utilizing the precision machining technology cultivated through mold manufacturing.
-
1968
Started export of precision plastic molds to the U.S.A., Canada, Mexico and Singapore.
-
1969
Purchased a 26,400-m² plant site in Ogori City, Fukuoka Prefecture, in preparation for business expansion.
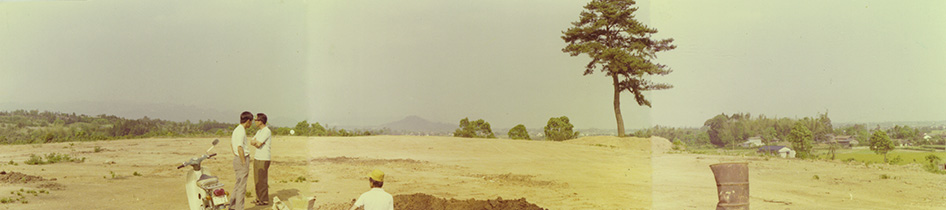
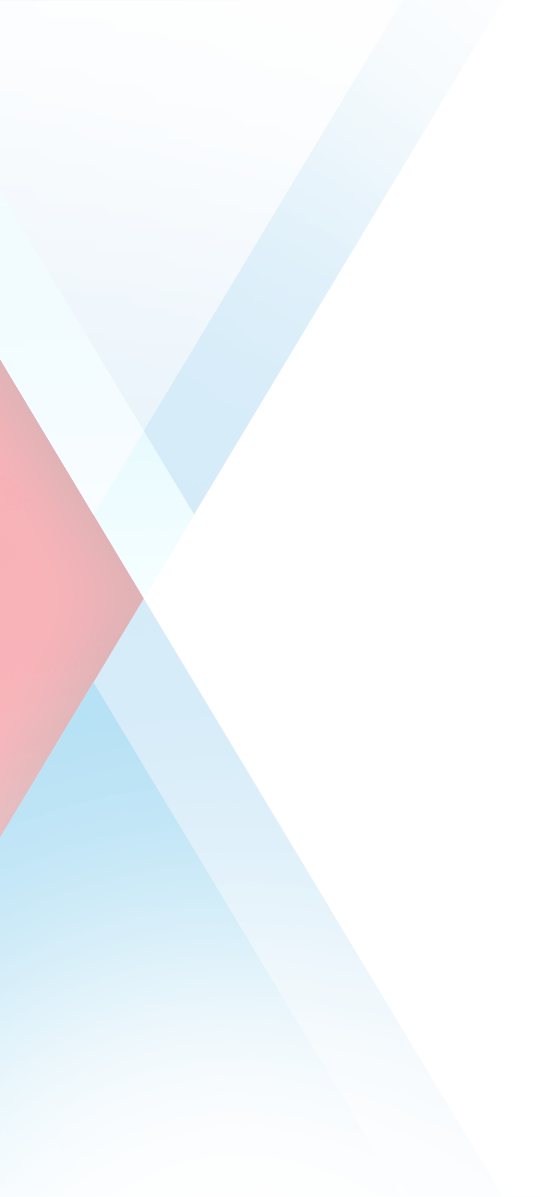
-
1971
Export growth owing to its high reputation as a Company “exceeding international standards”
Participated in the “National Plastic Exhibition” held in Chicago for the first time as a company in the Japanese mold industry.
-
Opened a representative office in Singapore.
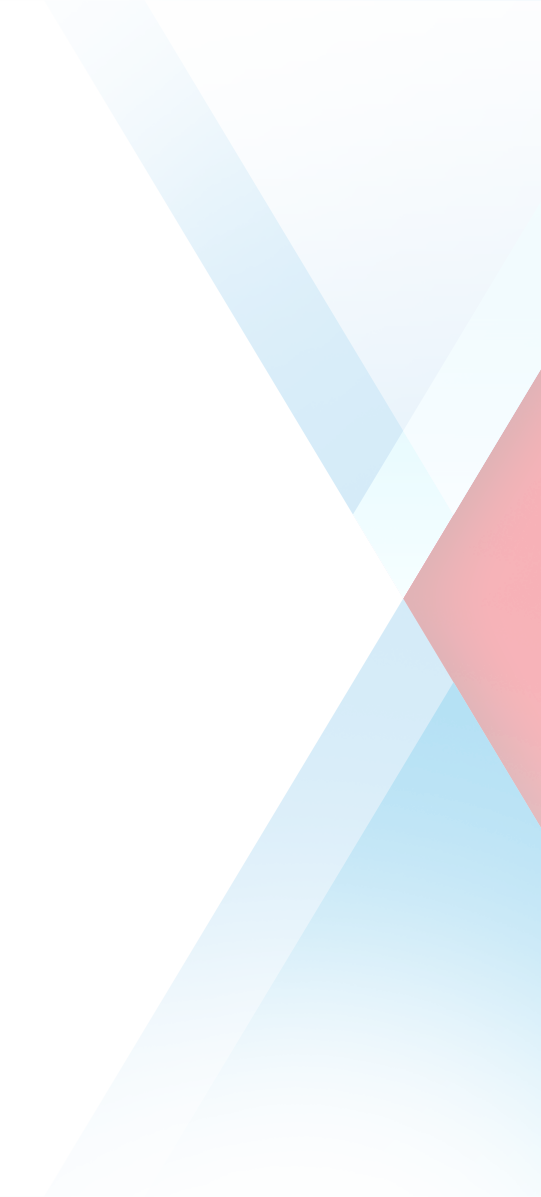
-
-
1972
Developed an automatic packaging system for molding semiconductors.
-
Participated at the Japan Plastic Exhibition for the first time as a manufacturer specializing in molds.
Opened the Tokyo Branch Office.
molded products
1973 - 1987
To start manufacturing plastic molded products
Dai-ichi Seiko forayed into the field of mass production of plastic molded products. It set up production bases in Fukuoka, Tokyo, Yamanashi through OEM production and spin-off management, and it established Singapore Dai-ichi Pte. Ltd. as its first overseas business establishment. In the 1980s, we released the world's first fully automatic semiconductor molding equipment, GP-SYSTEM. In the mid-1980s, the Dai-ichi Seiko Group exceeded 10 billion yen in sales, further deepening its business and expanding its scale.
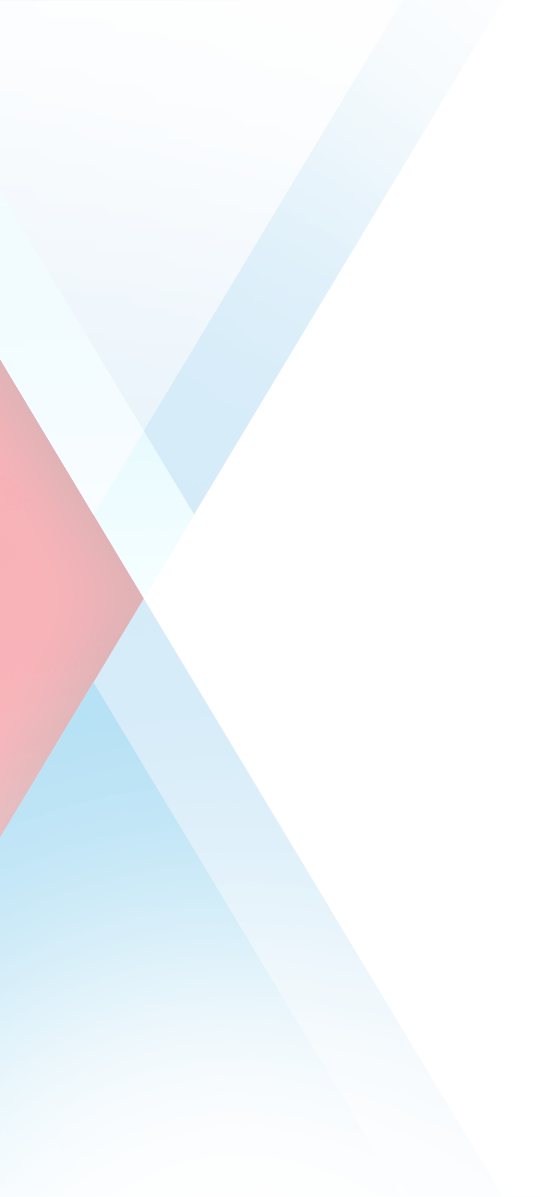
-
-
1973
Challenge of becoming a precision component manufacturer
Proposed mass production of plastic molded products to customers and started contract manufacturing of precision plastic components.
1973
Entry into contract manufacturing of connectors and molded products and expansion of business
Dai-ichi Seiko began OEM production of precision plastic components in the early 1970s, when it received orders for mass production of molded connectors using its own molds. From that time, Dai-ichi Seiko was commissioned to mass-produce a wide variety of products and deepened its technical expertise in integrated production to produce higher precision and quality products and expand its business scale.
-
Precision plastic parts
-
Connectors (OEM production)
1960s
1970s
For electronic calculators (1960)
Used for the numerical display area of electronic calculators
For felt-tip pen holders(1960)
For cameras (1960)
Replacement of metal parts achieved by high levels of roundness and flatness
1980s
For cassette tapes (1980)
1990s
For floppy disk exterior (1991)
Used for floppy disk in/out slots
For VCRs (1997)
Shaft holders used for VCRs
For game consoles (1997)
For bicycles (1997)
2000s
Water meter (2002)
Produced from approximately 50 parts through various processes, including welding, press-fitting, printing and affixation
2010s
Forensic device (2010)
Microfluidic devices used for forensic-related analysis
-
Connectors (OEM production)
1970s
Various connectors for automobiles (1973)
Waterproof connectors commonly used near car engines to prevent problems caused by rain and mud
Drawer connectors (1973)
Used for general office equipment, such as fax machines, printers, cash registers and ATMs
Various connectors for consumer use (1976)
Used for a wide range of consumer products, including video cameras and other AV equipment
1980s
Various connectors for industrial use (1980)
Connectors used in industrial robots and other industrial devices
1990s
For stereos (1990)
0.5 mm pitch FPC connectors(1994)
Achieving mass production of 0.5 mm pitch connectors, which were considered difficult to manufacture at the time
Burn-in connector(1994)
ECU connector(1994)
0.3 mm pitch connector (1994)
Used for information-related equipment, such as video cameras and notebook PCs
2000s
Optical connectors(2001)
Optical connectors that achieve micron-level precision using thermoplastic resin
2010s
Automotive integrated connectors(2013)
Automotive connectors integrating multiple connectors that conform to the USCAR2 standard in the U.S.
-
-
-
Constructed a plant for mass production at the headquarters.
-
1974
Expansion into the U.S.A., the forefront of the electronics industry
Opened the Chicago Sales
Office to strengthen export to the U.S.A.
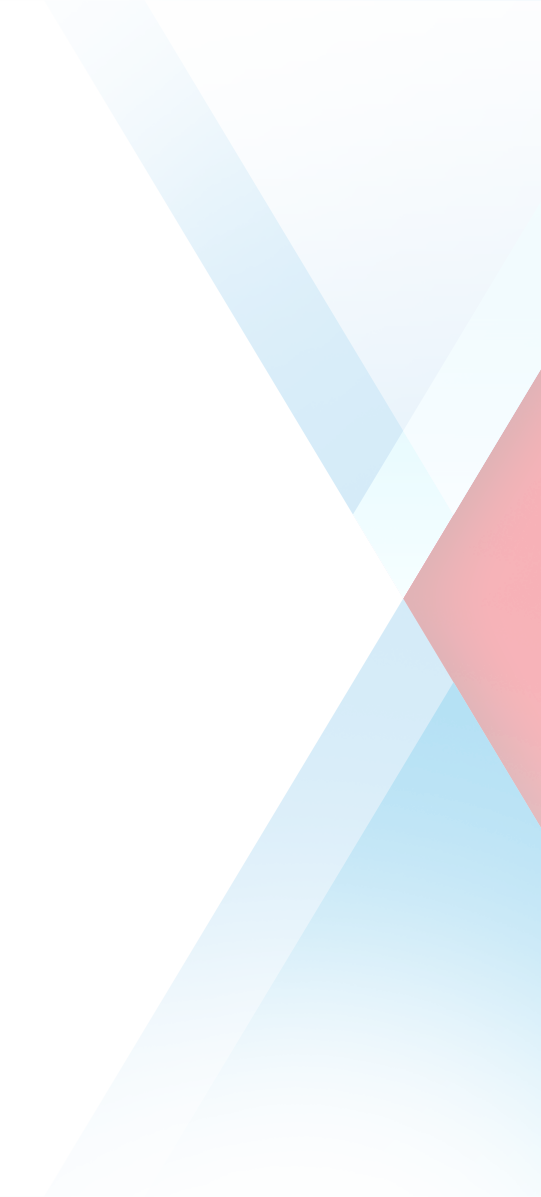
-
1976
Established Shuwa Seiko Co., Ltd., the first subsidiary, in Chikushino City, Fukuoka Prefecture.
1976
Established Shuwa Seiko Co., Ltd. in Chikushino City, Fukuoka Prefecture
Established Eikosha Co., Ltd. in Fuchu City, TokyoIn 1973, Dai-ichi Seiko began manufacturing plastic molded products for customers that had commissioned the company to manufacture molds, and this was the beginning of Dai-ichi Seiko's foray into the mass production of molded products. In March 1976, Dai-ichi Seiko established Shuwa Seiko Co., Ltd. to manufacture precision molds (Chikushino City, Fukuoka Prefecture), and in October 1976, it established Eiko-sha, Ltd. to mass produce connectors (Fuchu City, Tokyo). Subsequently, Dai-ichi Seiko formed a group of 13 domestic companies in the early 1980s through spin-off management. After establishing the Ogori Plant (Fukuoka Prefecture) in 1982, the company expanded its production bases, including the Yamanashi Plant (Yamanashi Prefecture) in 1986, the Tachiarai Plant (Fukuoka Prefecture) in 1992, the Shimane Plant (Shimane Prefecture) in 2007 and the Okinawa Plant (Okinawa Prefecture) in 2020.
Expanding bases in Japan
1976
-
March 1976
Shuwa Seiko Co., Ltd.(Chikushino City, Fukuoka Prefecture)
-
October 1976
Eikosha Co., Ltd.(Fuchu City, Tokyo)
1978
-
September 1978
Nishikosha Co., Ltd.(currently Onojo Plant)(Onojo City, Fukuoka Prefecture)
1982
-
January 1982
Ogori Plant(Ogori City, Fukuoka Prefecture)
1986
-
January 1986
Yamanashi Plant(Yamanashi City, Yamanashi Prefecture)
1992
-
August 1992
Tachiarai Plant(Asakura District, Fukuoka Prefecture)
2011
-
January 2011
Shimane Plant(Matsue City, Shimane Prefecture, now I-PEX Shimane Co., Ltd.)
2020
-
January 2020
Okinawa Plant(Uruma City, Okinawa Prefecture)
2022
-
December 2022
Okinawa Innovation Center(Uruma City, Okinawa Prefecture)
-
-
-
Established Eikosha Co., Ltd., the first mass production subsidiary, in Fuchu City, Tokyo.
-
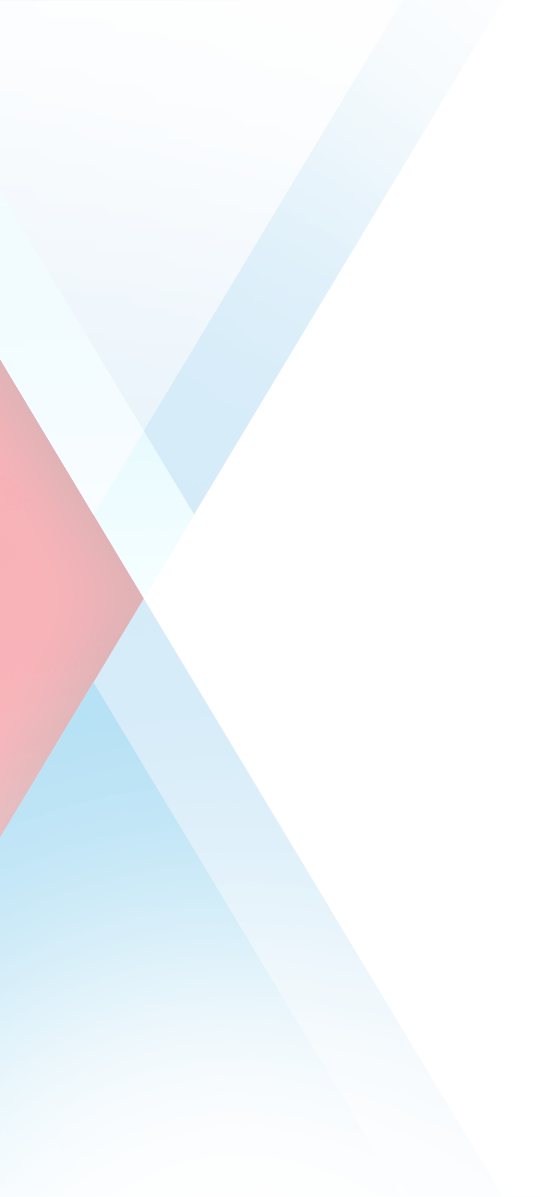
-
-
1979
Established the first overseas production base in Southeast Asia
Established Singapore Dai-ichi Pte. Ltd. (now I-PEX Singapore Pte Ltd) as the first overseas production base.
1979
Established Singapore Dai-ichi Pte. Ltd. as the first overseas production base
Active in attracting companies since the 1960s, Singapore had become the center of the electronics industry in the ASEAN region. In January 1979, Dai-ichi Seiko established Singapore Dai-ichi Pte. Ltd. for the purpose of manufacturing plastic molded products. This was the Dai-ichi Seiko Group's first full-scale overseas operation. After the Plaza Accord in 1985, Japanese companies shifted their production to Southeast Asia, and Dai-ichi Seiko was no exception, establishing production bases in the Philippines and Malaysia. After that, Dai-ichi Seiko, by a meandering path, continued to expand its business bases in Thailand, Indonesia and Vietnam.
Overseas expansion (Southeast Asia)
1979
-
January 1979
Singapore: Ang Mo Kio Plant(Singapore Dai-ichi Pte. Ltd.)
1987
-
August 1987
Singapore: Kallang Plant(Singapore Dai-ichi Pte. Ltd.)
1988
-
November 1988
Philippines Plant(Philippine, D-I Inc.)
1989
-
June 1989
Malaysia: Johor Bahru Plant(MDI Sdn. Bhd.)
1991
-
March 1991
Singapore: Woodland Plant(Hitool (s) Pte. Ltd., now I-PEX Singapore Pte Ltd, Woodland Plant)
1992
-
May 1992
Philippines: Cebu Plant(Cebu Dai-ichi, Inc.)
1993
-
October 1993
Singapore: Yishun Plant(Singapore Dai-ichi Pte. Ltd, Yishun Plant, now I-PEX Singapore Pte Ltd, Yishun Plant)
1994
-
February 1994
Philippines: Laguna Plant(Laguna Dai-ichi, Inc., now I-PEX Philippines Inc.)
2000
-
June 2000
Thailand: Chonburi Plant(Thai Dai-ichi Seiko Co., Ltd., now I-PEX (Thailand) Co., Ltd.)
-
December 2000
Indonesia: Bintan Plant(PT. Pertama Precision Bintan, now PT IPEX Indonesia Inc)
2006
-
June 2006
Vietnam: Ho Chi Minh Plant(Vietnam Dai-ichiSeiko Co., Ltd., now I-PEX Viet Nam Co., Ltd.)
2018
-
October 2018
Malaysia: New Johor Bahru Plant(Dai-ichi Seiko (M) Sdn. Bhd, now IPEX Global Manufacturing (M) Sdn. Bhd.)
-
-
-
1980
Opening the door to the era of semiconductor mass production
Developed the world's first fully automatic semiconductor molding equipment “GP-SYSTEM.”
1980
Development of GP-SYSTEM, the world's first fully automatic semiconductor molding equipment
Development of GP-SYSTEM
The process of molding wired semiconductor chips with resin is an essential semiconductor manufacturing process for ensuring the reliability of semiconductors. After developing an automatic packaging system for this process in 1972, Dai-ichi Seiko made a number of technical studies to further improve the system and in 1980, completed the GP-SYSTEM, the world's first fully automatic semiconductor molding equipment. Since then, Dai-ichi Seiko has continued to supply the fully automatic semiconductor molding equipment to semiconductor manufacturers throughout the world. The equipment has undergone numerous upgrades and has been succeeded by the current GP-PRO SP series.
-
GP-MARK I (1980)
-
GP-PRO SP (2000)
-
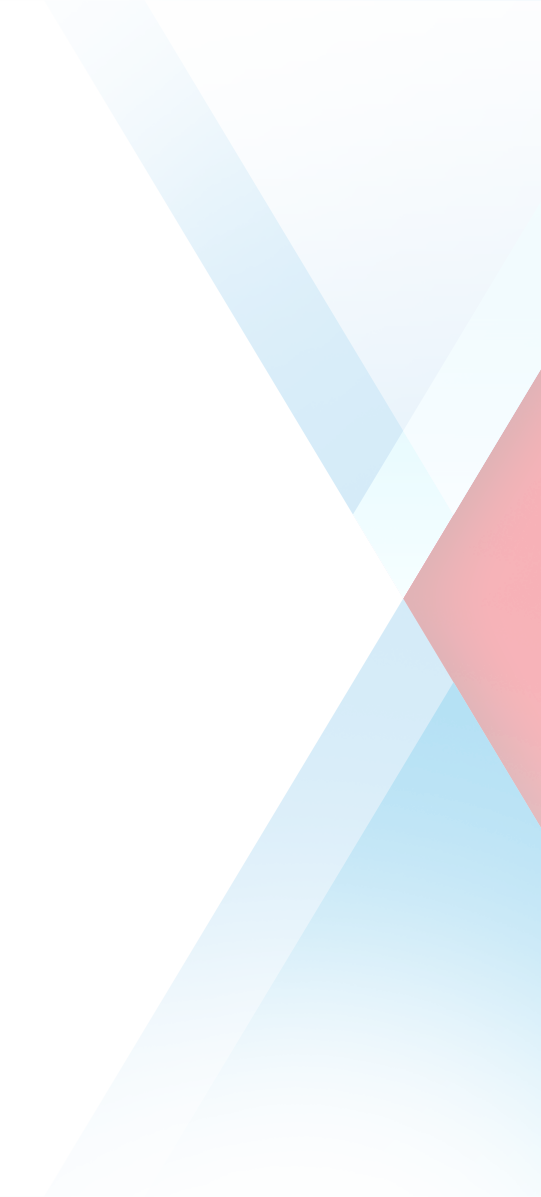
-
1981
Making Fukuoka as a business base for the future
Opened the Ogori Plant in Ogori City, Fukuoka Prefecture.
-
-
1986
Expanded into Yamanashi to establish Kai Seiko Co., Ltd.
-
-
1987
Opened a second plant in Singapore (Kallang).
global expansion
1988 - 2003
Borderless production and procurement
While focusing on the integrated production of connectors and electronic mechanical parts and the production and sale of semiconductor manufacturing equipment in Japan, Dai-ichi Seiko started commissioned production of automotive components in the Philippines. Through the development of the world's first micro-coaxial connector and entry into the HDD parts business, Dai-ichi Seiko promoted the development of new markets and business diversification while expanding its production system to Southeast Asia, China and North America to establish an optimum site production system.
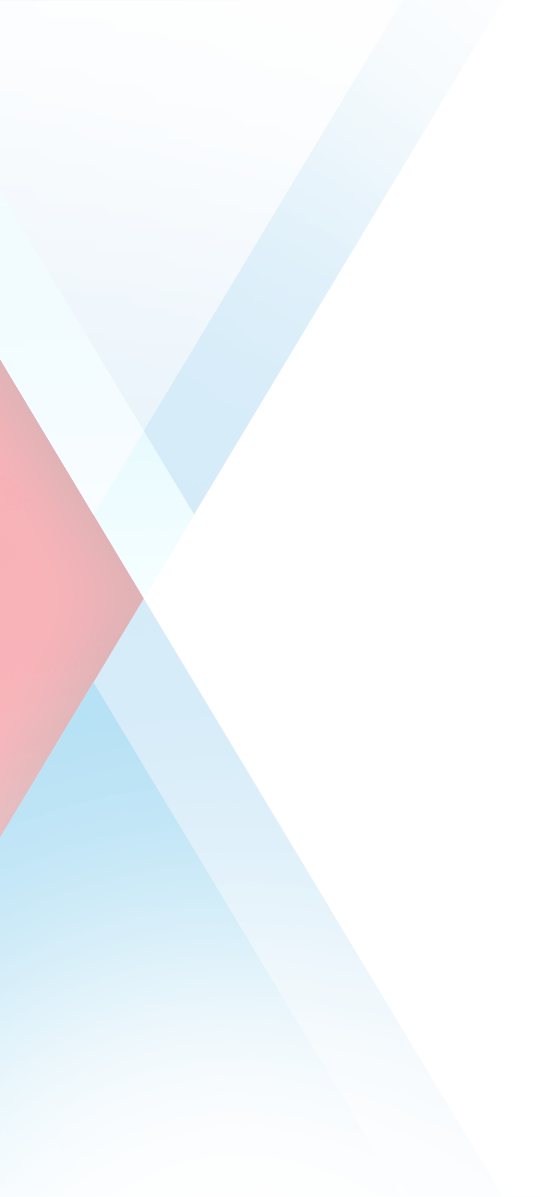
-
1988
Start of contract
manufacturing of automotive componentsEstablished Philippine, D-I Inc. in the Philippines as a production base.
1988
Start of contract manufacturing of automotive components
In 1987, Dai-ichi Seiko was commissioned by an automobile manufacturer to produce automotive components (ventilators) for North America. Since integrated production in the U.S. was difficult at the time, Dai-ichi Seiko manufactured the products domestically and exported them. In November 1988, it established Philippine, D-I Inc. as a manufacturing base in the Philippines. With the start of contract manufacturing of ventilators, the Dai-ichi Seiko Group entered the production of automotive components, including connectors, in earnest.
Entry into the automotive industry
1988
-
Ventilator
A unit part corresponding to the air outlet of an automobile air conditioner
1992
-
Power unit for door mirror
A part that is installed in the cover of the door mirror of an automobile and is operated electrically.
-
Tail light socket
Parts used in automobile tail lights
1995
-
Power window connector
A connector for controlling the opening and closing of automobile windows with a hand (door) switch
1998
-
Rotation sensor
A sensor that detects the rotation angle and speed of the crank and cam of an automobile engine.
2002
-
Wheel speed sensor
Used for ABS that electronically controls wheel locking due to sudden braking
2006
-
Card-type smart key
The world's first card-key by substrate in-mold molding
2014
-
Airbag sensor
A sensor installed in automobiles to detect collisions
-
-
-
Released the “GP-Zett,” a fully automatic semiconductor molding equipment for clean rooms.
-
-
1989
Established MDI Sdn. Bhd. in Malaysia (Johor Bahru) as a production base.
-
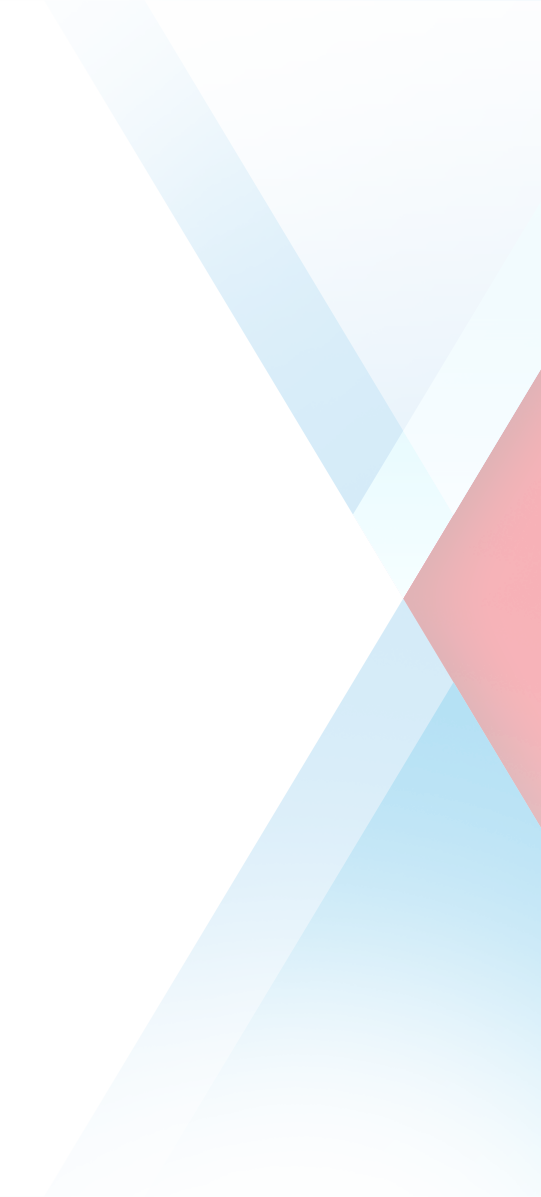
-
-
1990
Developed a fully automatic IC lead inspection machine.
-
-
1991
Established Hitool (s) Pte. Ltd. (now I-PEX Singapore Pte Ltd, Woodlands Plant) in Singapore (Woodlands) as a production base.
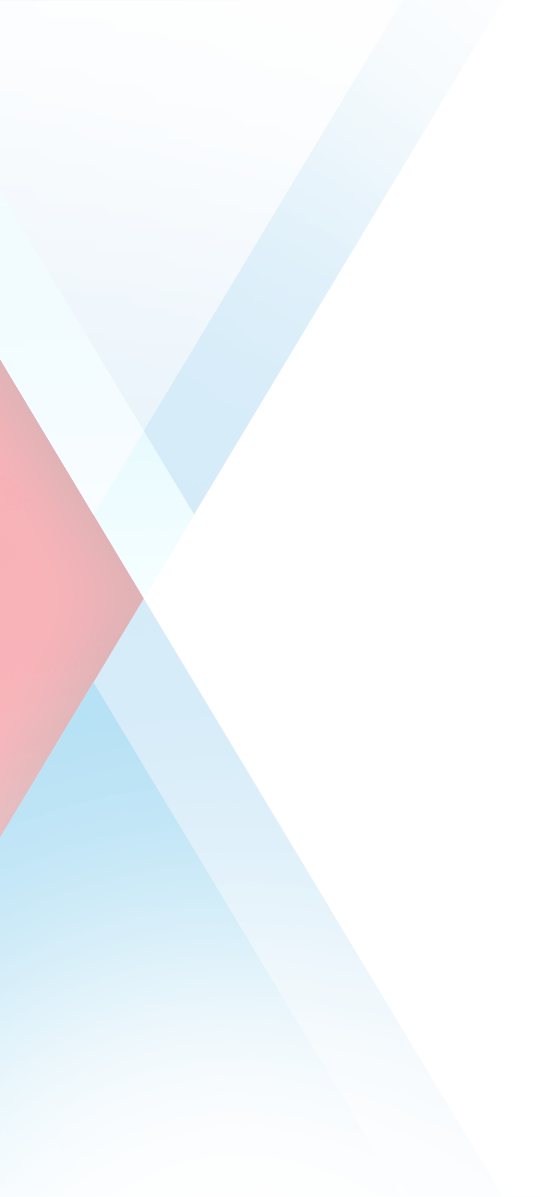
-
-
1991
Expansion of production bases to China
Established Shanghai Dai-ichi Mould & Plastics Co., Ltd. (now I-PEX Precision Mold & Plastics (Shanghai) Co., Ltd.) in Shanghai, China, as a production base.
1991
Established Shanghai Dai-ichi Mould & Plastics Co., Ltd.(present I-PEX Precision Mold & Plastics (Shanghai) Co., Ltd.) in Shanghai, China, as a production base.
In August 1991, when China was shifting from a planned economy to a market economy, Dai-ichi Seiko established, Shanghai Dai-ichi Mould & Plastics Co., Ltd. (Shanghai Plant 1). Since it was Dai-ichi Seiko's basic policy to train new graduates and develop them into useful human resources, the company started as a solely owned company rather than a joint venture with a local company. After that, Dai-Ichi Seiko set up Hong Kong Dai-ichi Seiko Co., Ltd. in 2003, Shanghai Plant 2 in 2004, Dong Guan Dai-ichi Seiko Mold & Plastics Co., Ltd. (Dongguan Plant) in 2005 and the Shanghai Technical Center (Shanghai Plant 3), its first overseas engineering base, in 2017.
-
In April 1991, Shanghai Plant 1 (Shanghai Dai-ichi Mould & Plastics Co., Ltd., now I-PEX Precision Mold & Plastics (Shanghai) Co., Ltd.)
-
March 2005 the Dongguan Plan (Dong Guan Dai-ichi Seiko Mold & Plastics Co., Ltd., now I-PEX Precision Mold & Plastics (Dongguan) Co., Ltd.)
-
February 2004 Shanghai Plant 2
-
November 2020 Shanghai Plant 3
-
-
1992
Established Cebu Dai-ichi, Inc. in the Philippines (Cebu) as a production base.
-
1993
Started operations at the new plant of Singapore Dai-ichi Pte. Ltd. (now I-PEX Singapore Pte Ltd, Yishun Plant) in Singapore (Yishun).
-
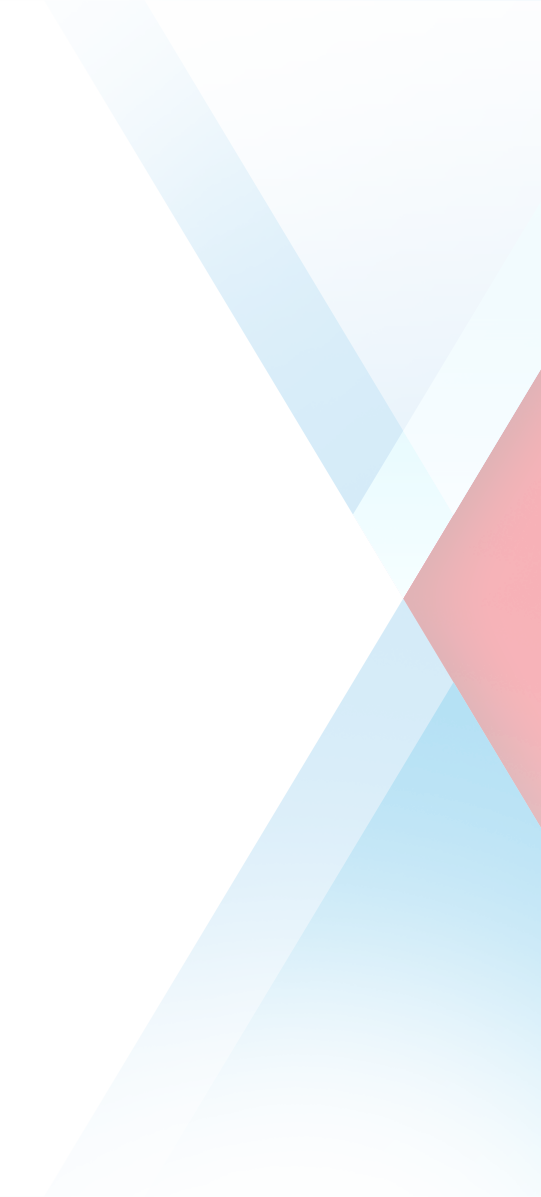
-
1994
Established Dai-ichi Seiko America, Inc. (now I-PEX USA Components Inc.) in California (San Jose), U.S.A.
-
Established Laguna Dai-ichi, Inc. (now I-PEX Philippines Inc.) in the Philippines (Laguna) as a production base.
-
-
-
1995
Development of the world’s first micro-coaxial connector
Received an inquiry for micro-coaxial connectors for notebook PCs.
Developed the micro-coaxial connector CABLINE I® series the following year.1995
Evolution into a connector manufacturer
In 1995, I-PEX Co., Ltd., a fabless manufacturer prior to its business merger with Dai-ichi Seiko Co., Ltd., worked on the development of micro-coaxial connectors for notebook PCs with high-quality displays at the request of IBM of the U.S.A. Such a technologically advanced connecting system did not exist at the time. In cooperation with Dai-Ichi Seiko's manufacturing engineering department, I-PEX successfully developed the “CABLINE® I,” the world's first micro-coaxial connector in 1996. The product was subsequently made into a series and used in many information devices, and I-PEX became well known in the industry as a manufacturer of micro-coaxial connectors.
Development of I-PEX brand connector
1996
-
CABLINE® I
The world's first micro-coaxial cable connector developed for notebook PCs
2001
-
MHF® I
For communication cards, the solderless connection method “i-Fit®” is adopted to achieve uniform electrical characteristics.
2008
-
CABLINE®-VS
Approved by the industry standardization body VESA as the standard connector for laptop display connections
2010
-
EVAFLEX® 5
Connectors for TV panels that improve productivity with one-action mating and locking
2014
-
ISH
Automotive connectors used for headlamps, etc. that can withstand high temperatures of 125°C and have excellent vibration resistance
2016
-
NOVASTACK®-35 HDP
Board-to-board (FPC) connectors with excellent EMI (electromagnetic interference) shielding
2021
-
LIGHTPASS®
Active optical module that converts optical and electrical signals
2022
-
DUALINE®
Twinax cable connector ideal for high-speed transmission in servers, etc.
-
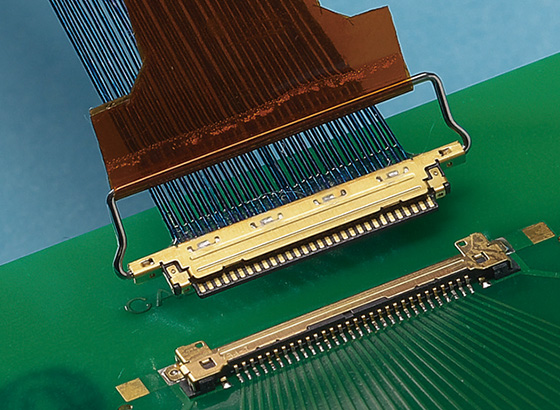
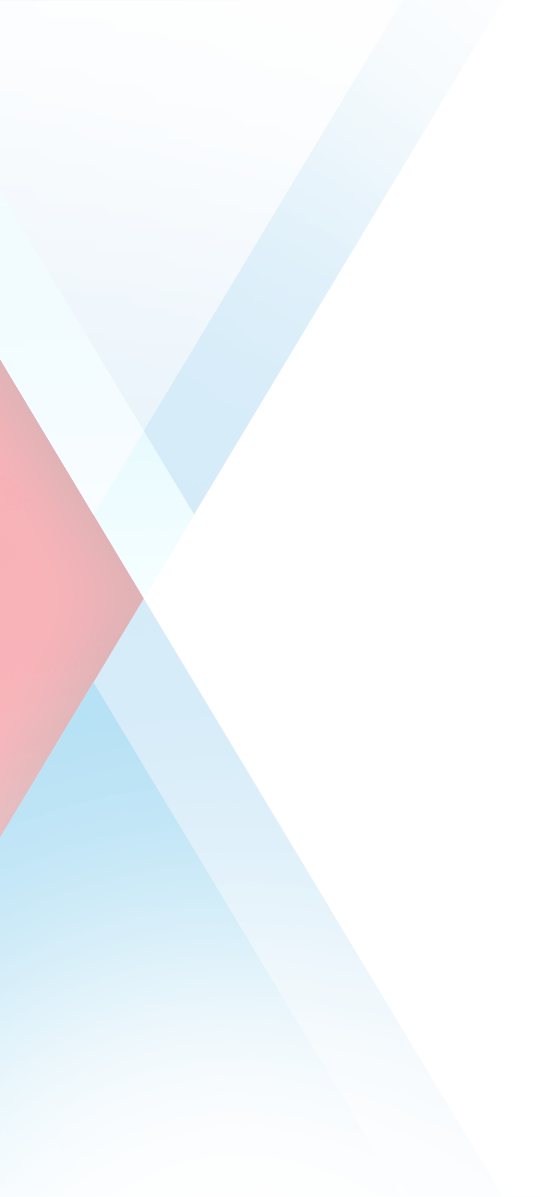
-
1997
Start of production of hard disk parts
Started the world’s first mass production of ramp, one of the important parts for HDDs.
1997
Start of production of hard disk parts
A ramp, one of the important parts for hard disk drives (HDDs), is used in HDDs with a load/unload mechanism that prevents contact between the disk surface and the magnetic head, and its manufacture requires ultraprecision dimensional control. In 1997, Dai-Ichi Seiko was engaged in the joint development of a ramp at the request of IBM and was the first in the world to achieve its mass production. Since then, the company has been manufacturing various mechanical parts for HDDs, including latches for braking actuators and slits for fixing parts, and supplying them to the market.
-
Ramp (1996)
-
Latch (1997)
-
Air Spoiler (2006)
-
-
-
1998
Started mass production of Angle sensor, an automotive component.
Opened the Taiwan Office in Taiwan (Kaohsiung).
1999
Opened the Thai Office in Thailand (Bangkok).
-
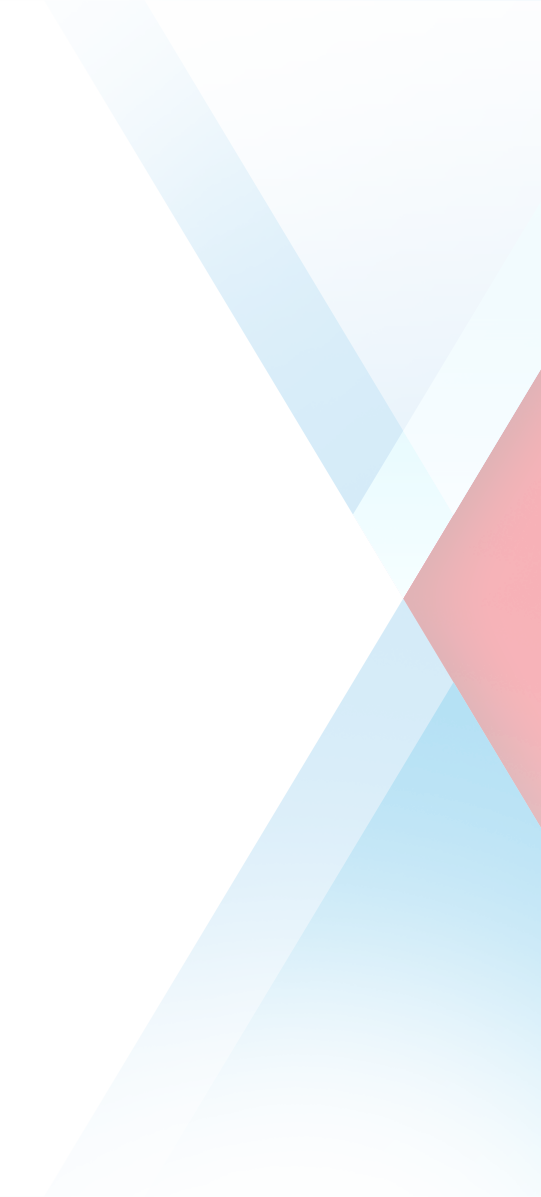
-
-
2000
Established Thai Dai-ichi Seiko Co., Ltd. (now I-PEX (Thailand) Co., Ltd.) in Thailand (Bangkok) as a production base.
-
Opened the Malaysia Office in Malaysia (Ipoh).
-
-
2000
Expansion of production bases in the U.S.A.
Established Touchstone Precision, Inc. (now I-PEX USA Manufacturing Inc.) in Alabama, U.S.A.,
as a production base2000
Established Touchstone Precision, Inc. in Alabama, U.S.A
Overseas expansion (U.S.A.)
In December 2000, Dai-Ichi Seiko established Touchstone Precision, Inc. in Auburn, Alabama, U.S.A., in order to start up a plant for automotive components and started its operation in 2002. This was Dai-ichi Seiko's first manufacturing base in North America and its first full-scale entry into a developed country. In 2013, Dai-ichi Seiko started mass production of in-vehicle PCB connectors designed in-house. In 2015, it extended the plant in anticipation of business expansion, making it an important strategic base for the Dai-ichi Seiko Group’s automotive components business.
-
Alabama factory at the time of establishment
Group photo at the time of the establishment of the Alabama plant
-
Local newspaper at the time of expansion into the United States
(page 1, President Hideki Konishi)
-
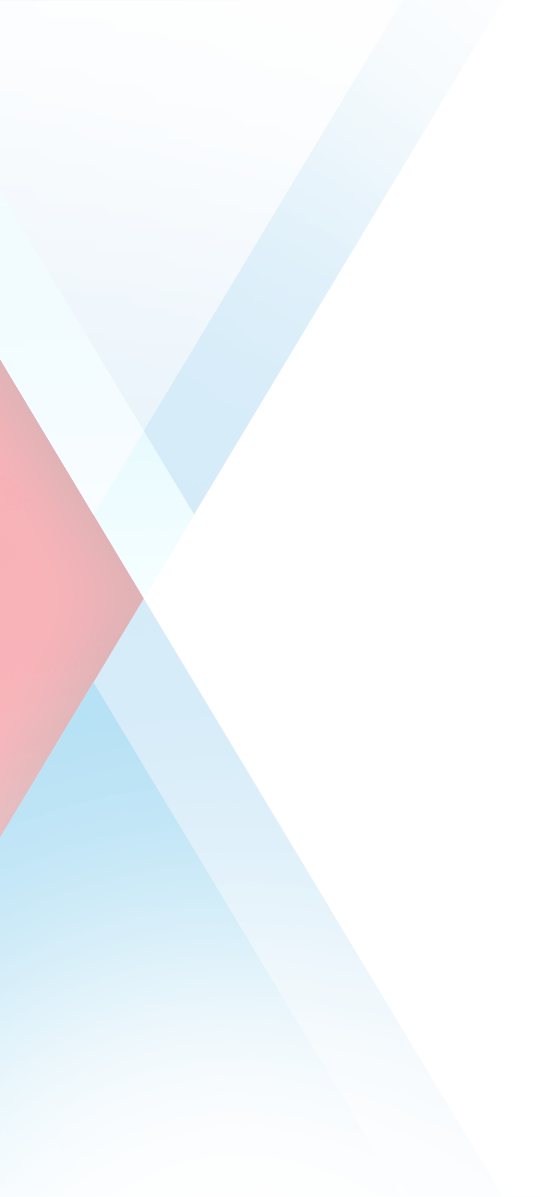
-
-
2000
Established PT. Pertama Precision Bintan (now PT IPEX Indonesia Inc.) in Indonesia (Bintan Island) as a production base.
-
2001
Started mass production of the RF coaxial connector MHF® series.
Opened the Shanghai Office in China (Shanghai).
2002
Established Hong Kong Dai-ichi Seiko Co., Ltd. in China (Hong Kong).
-
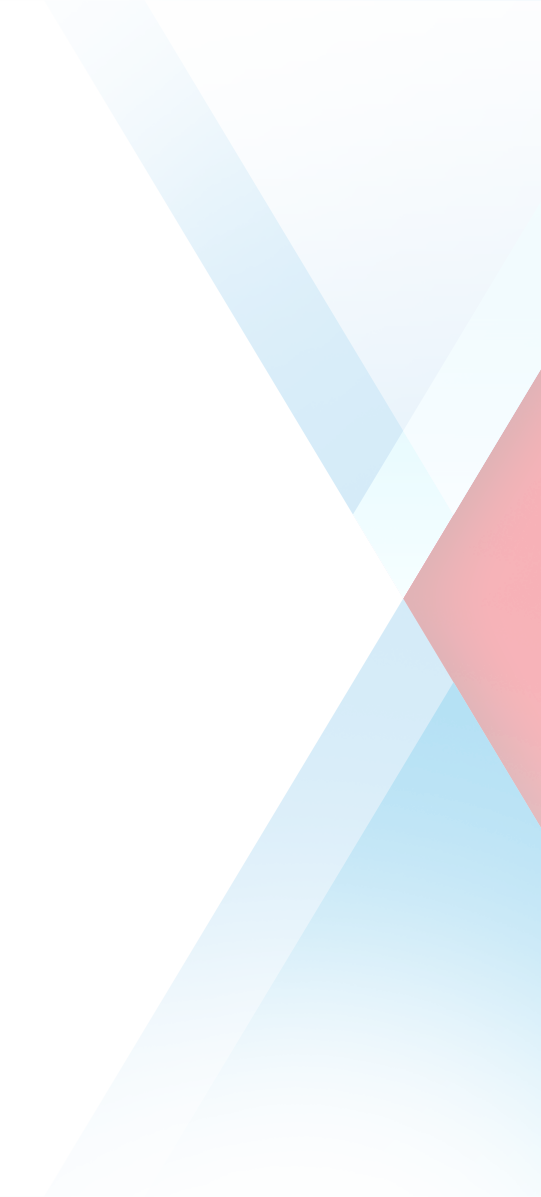
perfection in precision
2004 - 2019
Becoming a connector manufacturer with integrated production
Dai-ichi Seiko shifted from an OEM manufacturer to a connector manufacturer after the merger with I-PEX Co., Ltd.. In particular, by making a name for itself as a fine-wire coaxial connector manufacturer, it has been driven the development of its business and the company has been listed on the JASDAQ Security Exchange and on the First Section of the Tokyo Stock Exchange. On the other hand, the company focused on developing new products such as the world's first Electrostatic Capacitance Torque Sensor and Smell Sensor.
-
2004
Integration of development, manufacturing and sales
Acquired I-PEX Co., Ltd., an innovator of high-speed, wide-area transmission connectors, as a subsidiary.
2004
Move to new growth stage through business integration
-
Integration of development, manufacturing and sales
In July 2004, Dai-ichi Seiko acquired approximately two-thirds of the shares of the connector manufacturer I-PEX Co., Ltd. to integrate its operations. With this opportunity, the company moved to a new growth stage, aiming to become a leading company group with both technological development and manufacturing capabilities in the global electronic components market.
-
I-PEX Co., Ltd.
-
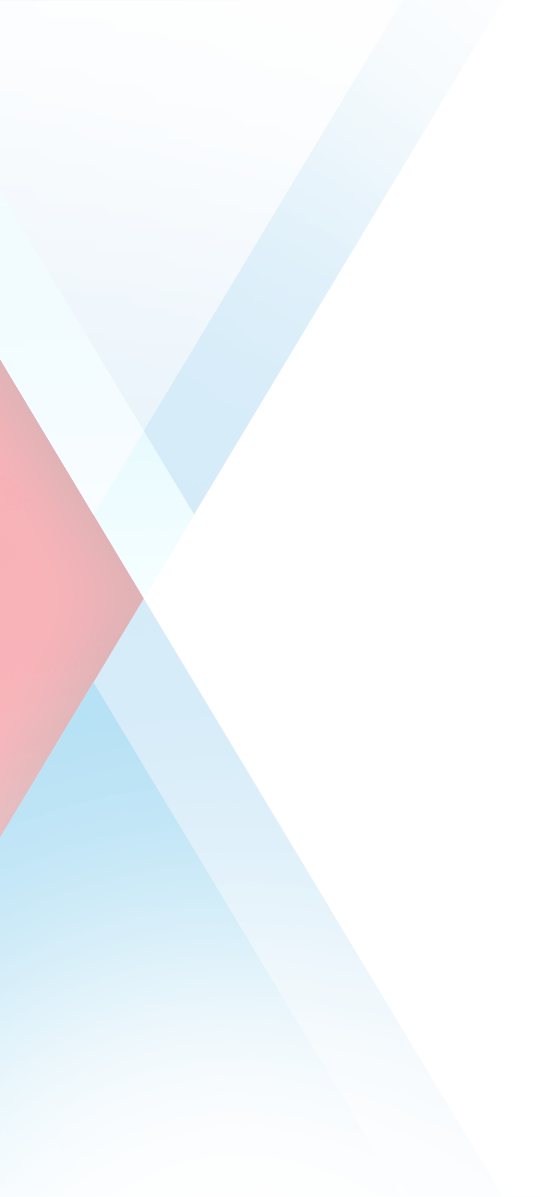
-
2005
Established Dong Guan Dai-ichi Seiko Mold & Plastics Co., Ltd. (now I-PEX Precision Mold & Plastics (Dongguan) Co., Ltd.) in China (Dongguan) as a production base.
Established DJ Precision Co., Ltd. as a joint venture with Japan Aviation Electronics Industry, Ltd.
Opened the Hachioji Technical Center.
-
-
-
2006
Established Vietnam Dai-ichi Seiko Co., Ltd. (now I-PEX Viet Nam Co., Ltd.) in Vietnam (Ho Chi Minh City) as a production base.
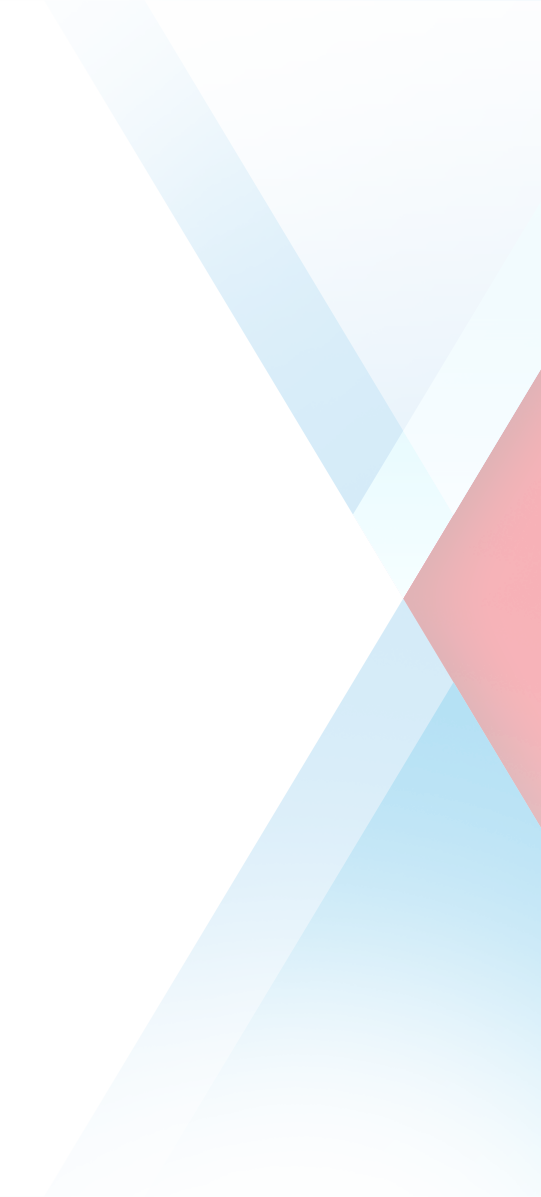
-
-
2006
Accelerating growth with stock listing
Listed on the JASDAQ Securities Exchange.
2006
Listed on the JASDAQ Securities Exchange
Accelerating growth with stock listing
In November 2006, Dai-ichi Seiko listed its stock on the JASDAQ Securities Exchange. Taking this opportunity, the company introduced a business headquarters system and strengthened its development and manufacturing systems and its integrated production system. In March 2011, Dai-ichi Seiko was listed on the First Section of the Tokyo Stock Exchange. (Transferred to the Tokyo Stock Exchange's Prime Market on April 4, 2022) In January of the following year, the company entered into a merger with I-PEX Co., Ltd. and Techno Dai-ichi Co., Ltd., aiming to further develop through strengthened cooperation among manufacturing, sales, technology and management.
-
November 2006 Listed on JASDAQ
-
March 2011 Ceremony at the time of listing on the Tokyo Stock Exchange
-
Tokyo Stock Exchange electronic bulletin board announcing Daiichi Seiko's first section listing
-
-
-
2007
Established Matsue Dai-ichi Seiko Co., Ltd. (now I-PEX Shimane Inc.) in Matsue City, Shimane Prefecture.
-
Established I-PEX France Sarl (now I-PEX Europe Sarl) in France.
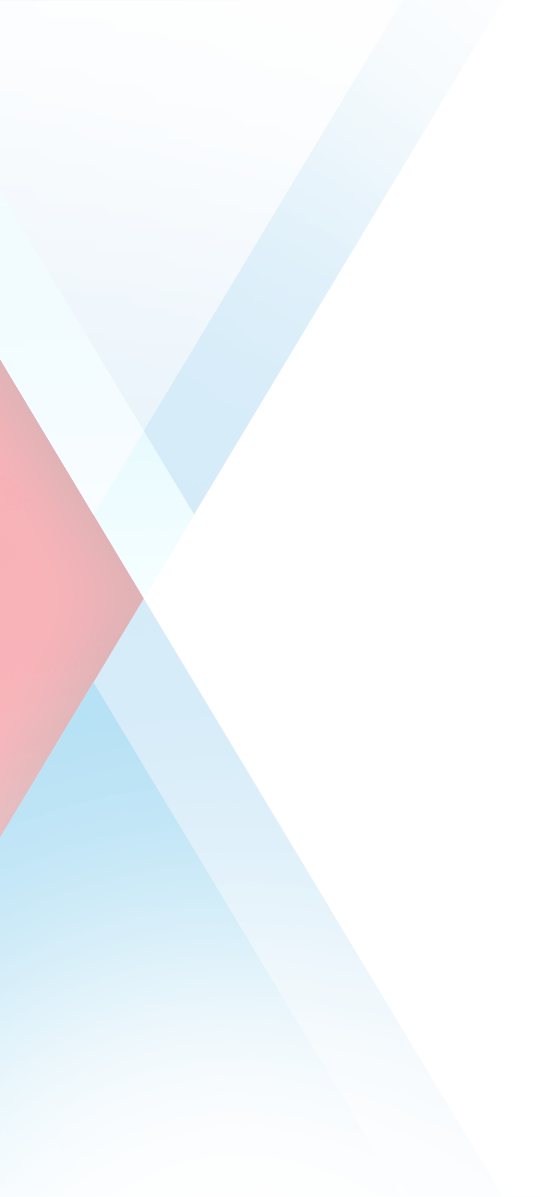
-
-
2009
To become a manufacturer that leads the global standards
The CABLINE®-VS micro-coaxial connector
was certified as a VESA standard.
-
2010
Started mass production of the FPC/FFC connector EVAFLEX® series.
-
-
2011
Opened the Shizuoka Office (now Shizuoka R&D Center) in Shizuoka City, Shizuoka Prefecture.
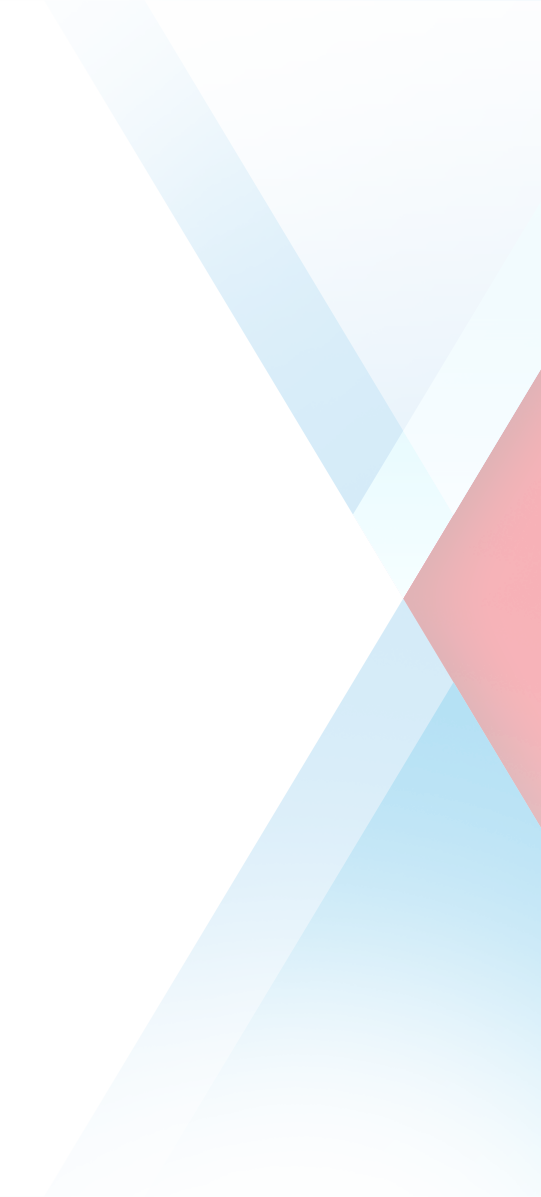
-
Listed on the First Section of the Tokyo Stock Exchange.
-
-
Started the automotive connector business.
-
-
2014
Development of new fields with proprietary sensor technology
Released the electrostatic capacitive torque sensor ESTORQ®.
2014
Released the Electrostatic Capacitance Torque Sensor “ESTORQ®”
As a new business initiative, Dai-ichi Seiko developed MEMS* devices using piezoelectric thin films, starting with the development of the world's first electrostatic capacitance torque sensor in 2014. The company commercialized earthquake detectors and smell sensors equipped with this sensor. In 2022, to further expand its MEMS business, the company acquired two companies with the single-crystal piezoelectric thin film technology, KRYSTAL, Inc. and Micro Innovators Laboratory, Inc., as subsidiaries. Subsequently, the two companies were merged into a new company, I-PEX Piezo Solutions Inc., to develop a MEMS foundry business from 2023.
* MEMS =Micro Electro Mechanical Systems--A MEMS device is a micro device that integrates electrical circuits and fine mechanical structures on a wafer.-
Electrostatic Capacitance Torque Sensor “ESTORQ®” (2014)
Smell Sensor “noseStick®”(2020)
-
Smell Sensor “nose@MEMS®”(2019)
-
Gripper for connector automatic mating robots “ES-Gripper®”(2017)
-
-
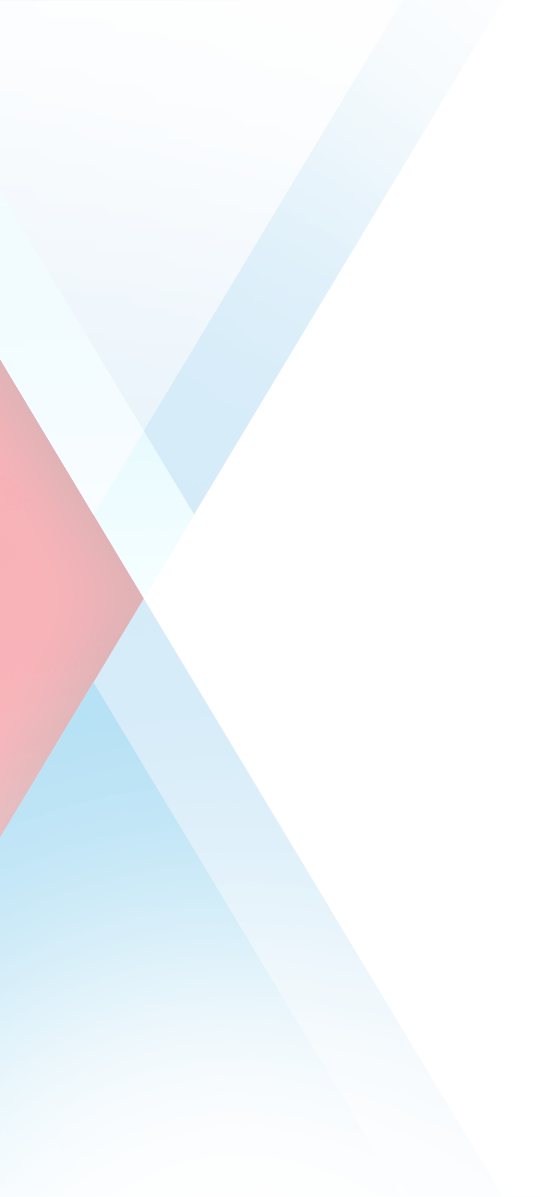
-
2015
Opened the Detroit Office of Dai-ichi Seiko America, Inc. (now I-PEX USA Components Inc.) in Michigan, U.S.A.
-
-
2016
Started mass production of the board to board (FPC) connector NOVASTACK® series.
-
Opened the Heiwa Laboratory (now Shizuoka R&D Center Heiwa Test Site) in Shizuoka City, Shizuoka Prefecture.
-
-
2018
Developed a smell sensor utilizing the MEMS technology nose@MEMS.
-
-
2019
Established Dai-ichi Seiko (M) Sdn. Bhd. (now IPEX Global Manufacturing (M) Sdn. Bhd.) in Malaysia (Johor Bahru) as a production base.
Established I-PEX Global Operations, Inc. in Tomigusuku City, Okinawa Prefecture.
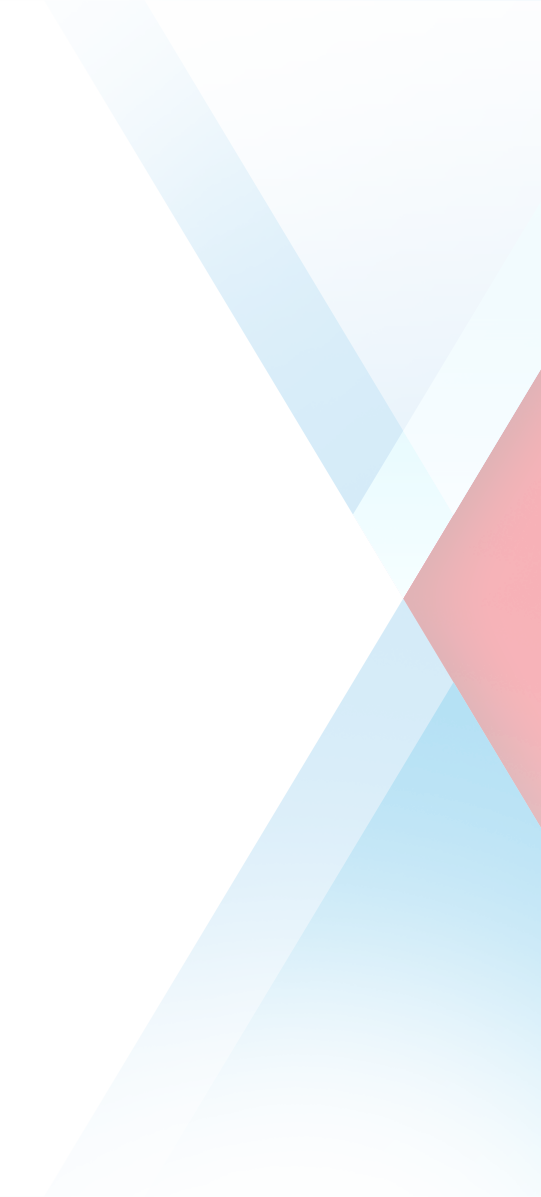
To be the Sharpest
2020 -
The Sharpest to the world
Dai-ichi Seiko has made a new start as an “Innovative Product development & Engineering solutions eXpert” by changing its company name to I-PEX Inc., and it started full-scale operation of the I-PEX Campus in Ogori City, Fukuoka Prefecture, as the core center of the Group's engineering departments. I-PEX formulated the “I-PEX Vision 2030,” a medium- to long-term management plan with the aim of evolving into a new business model. On the occasion of its 60th anniversary, I-PEX stepped up to the challenge toward the next era.
-
-
2020
Opened the I-PEX Campus in Ogori City, Fukuoka Prefecture.
2020
Opened the I-PEX Campus in Ogori City, Fukuoka Prefecture
Dai-ichi Seiko opened the I-PEX Campus, which was under development on the former site of the Kyushu Institute of Information Sciences Ogori Campus in Ogori City, Fukuoka Prefecture, in June 2020. The development & design, engineering & development and staff departments, which had been dispersed between the Ogori Plant and the Onojo Plant, moved to the I-PEX Campus Main Building, which was renovated from the former university building, and the Tech Forest mold manufacturing plant was completed on the I-PEX Campus in December of the following year. The I-PEX Campus, where the mold manufacturing departments of both plants were consolidated, became the core center of the Group's engineering departments.
-
-
Established Okinawa Plant in Uruma City, Okinawa Prefecture.
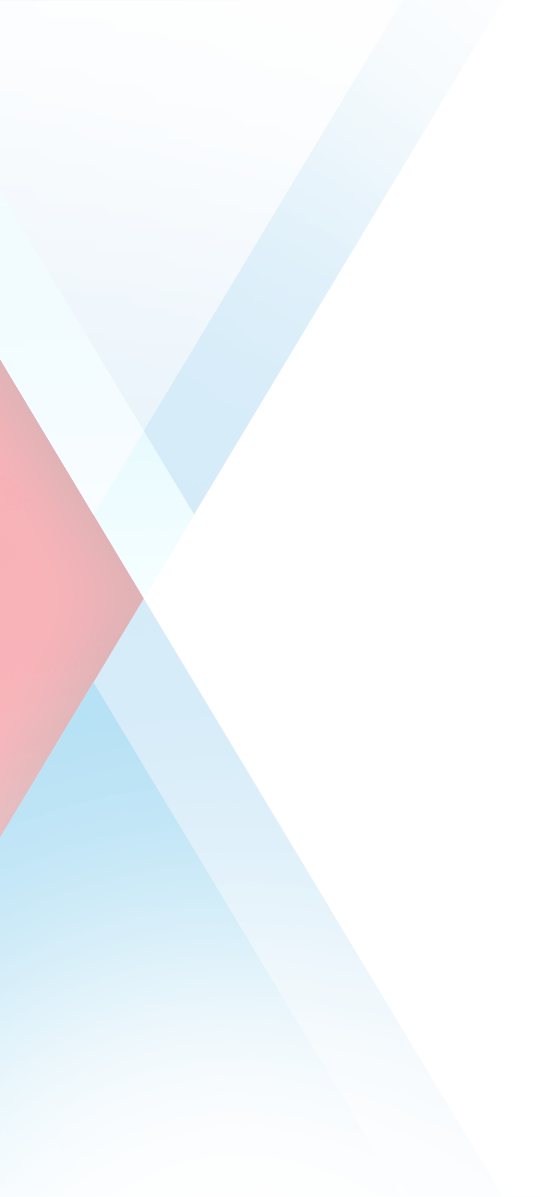
-
-
Rebuilding CI as a global brand
Changed the trade name to I-PEX Inc.
2020
Formulated CI and changed company name to I-PEX
In April 2018, Dai-ichi Seiko's Board of Directors launched the CI Project for future growth, and in December 2019, the following year, the CI statement and the corporate vision were formulated. In August 2020, the company name was changed from Dai-ichi Seiko Co., Ltd. to I-PEX Inc. in order to clarify the company's vision and enhance global brand recognition, and the corporate brand was unified into I-PEX.
-
Brand image with the I-PEX tagline “To be the Sharpest”
-
Nihon Keizai Shimbun Advertisement(August 3, 2020)
-
-
2021
Completed the Tech Forest mold manufacturing plant on the I-PEX Campus.
2022
Formulated “I-PEX Vision 2030,” a medium- to long-term management plan.
2022
Formulation of medium- to long-term management plan “I-PEX Vision 2030”
-
In February 2022, I-PEX has envisioned its vision for 2030 as becoming an “Innovative Product development & Engineering solutions eXpert”, a company with technical capabilities to implement “digital manufacturing”. To realize this vision, six points of materiality were set, including “Contribute to a safe and comfortable digital society through innovation”, “Transform the business structure and expand our field of business”, “Build an optimal manufacturing system and promote capital cost and cash flow management” which are to be comprehensively addressed by the entire Group.
-
I-PEX Vision 2030
-
-
-
Stock listing transferred to the Tokyo Stock Exchange’s Prime Market.
Opened the Yokohama Office in Yokohama City, Kanagawa Prefecture.
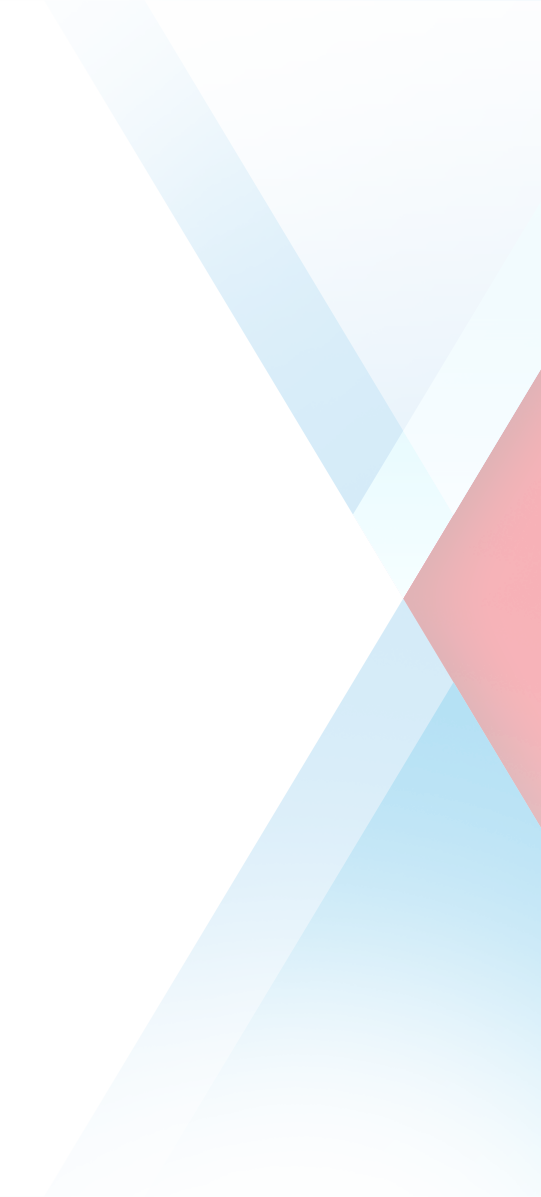
-
Issued the Group's first integrated report.
-
-
2023
Launch of the Piezoelectric MEMS Foundry
Established I-PEX Piezo Solutions for MEMS foundry business.
-
-
60th anniversary of founding on July 10, 2023
-
2024
Entered the Energy Solution Business with the RENERATH series of storage battery systems
-
-
2025
Delisted from the Tokyo Stock Exchange Prime Market following the MBO
-
-
Tokyo R&D Center relocated and expanded in Machida City, Tokyo