Front-Loading Design for Injection Molding
We introduce early-stage product design support, optimize operations, and maintain close communication with customers to ensure our solutions exceed expectations.
Our business is far from being a copycat.
We support your business, setting new standards and pushing the boundaries of manufacturing from Alabama.
As the I-PEX group, we excel in precision manufacturing technology. We have combined our skills in equipment development, design, and manufacturing for plastic parts and complex molded parts with pre and post molding processes.
This includes plastic injection molding and other mass production capabilities like stamping, plating, and assembly. These capabilities let us manage the entire process from start to finish, allowing us to meet the customer's needs for product quality, volume production, and lead times.
Our on-site field application engineers also support customers from an early design phase. With proposals to improve and stabilize quality and cost, we are commited to maximizing our customer's product value.
We don't just meet your requirements; we are committed to maximizing your value.
Design Optimization
We provide complete support right from the beginning of product development. Our goal is to improve the design and make manufacturing methods better and easier. This ensures that products are not only innovative but also efficiently produced, meeting high standards of quality and performance.
Mold Relief
Mold relief proposals are based on the results of mold flow analysis.
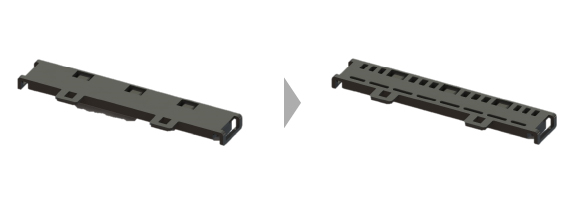
Simplified Design
Mold design proposals are based on the results of feasibility studies.
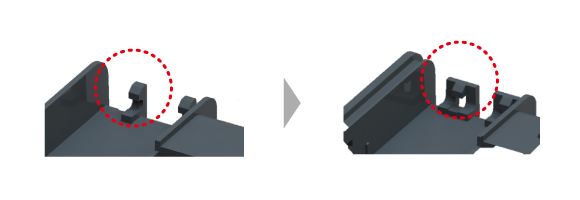
The best gate location was proposed based on the mold flow analysis data results.
Mold relief proposals are based on the results of the mold flow analysis.
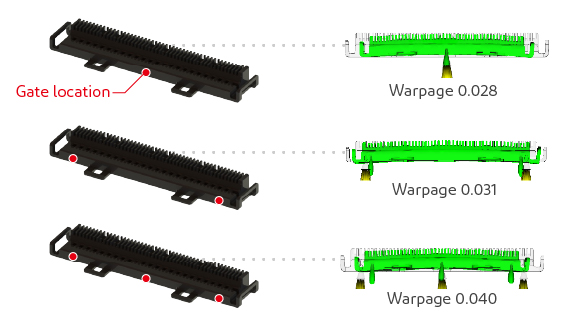
Design for Automation
Optimize terminal design to improve durability and allow for automated production.
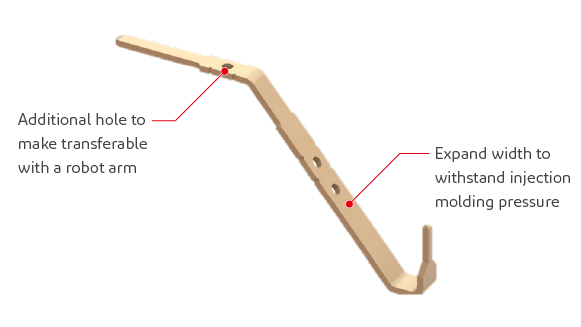
Engineering Expertise
Automated insert molding system helps stabilize production and improves quality, cost, and delivery of various automotive parts. The entire system is designed and fabricated in-house.
With our experience in tooling and automation maintenance, we know what it takes to continue meeting our customers' expectations.
Our Production Process
1. Design Review
Quality Cost- Feasibility study
- Moldflow analysis
- Structural analysis
- Design proposal
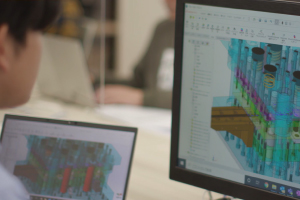
2. Tool Preparation
Quality Cost Delivery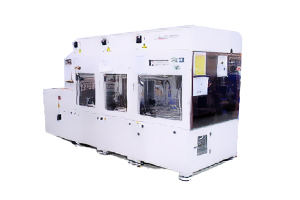
3. Stamping & Plating
Quality Cost Delivery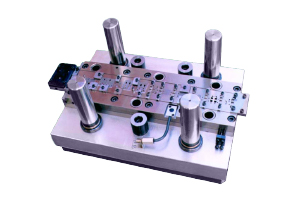
4. Molding
Quality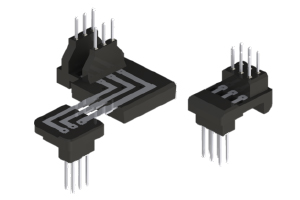
PPS Experience
High-quality PPS (Polyphenylene sulfide) products are crafted using advanced I-PEX mold design technology and extensive injection molding expertise. With half a century of industry experience and a global usage of 1,500 tons annually, these products exemplify precision engineering and reliability.
Capability to Make Flash-less Products
- Optimize air vent, air relief technology, and mold condition
- High stability and quality during mass production with molds
Capable of Less Than 0.05 mm Flash
Automated deflashing process with specific requirements:
- Blasting
- Heating
- Laser
- Trimming
Other Experiences
I-PEX offers a range of customizable processes designed to enhance our customer support. These processes can be integrated into our insert molding system or implemented as independent steps after the molding phase, ensuring flexibility and efficiency in meeting various project requirements.
Metal Welding
- Resistance welding
- Ultrasonic welding
Plastic Welding
- Heat welding
- Laser welding
Soldering
- Manual soldering
- Auto soldering
Potting
- Epoxy
- Fluorine elastomer
- Silicone
- Acrylic
Annealing
- Resistance welding
- Ultrasonic welding
Air Leak Test
- Differential pressure leak test
- Helium leak test
Vision Check
Heat treatment to improve resin material properties to prevent cracking or degradation of material.
IC Inspection
- IC Character
Automated Production Process
A streamlined and highly efficient production line has been designed for each product, integrating pre-processing, insert molding, and post-processing into a single, fully automated system. This setup not only enhances product quality but also ensures a consistent and stable production flow, reducing the potential for errors and improving overall manufacturing efficiency.
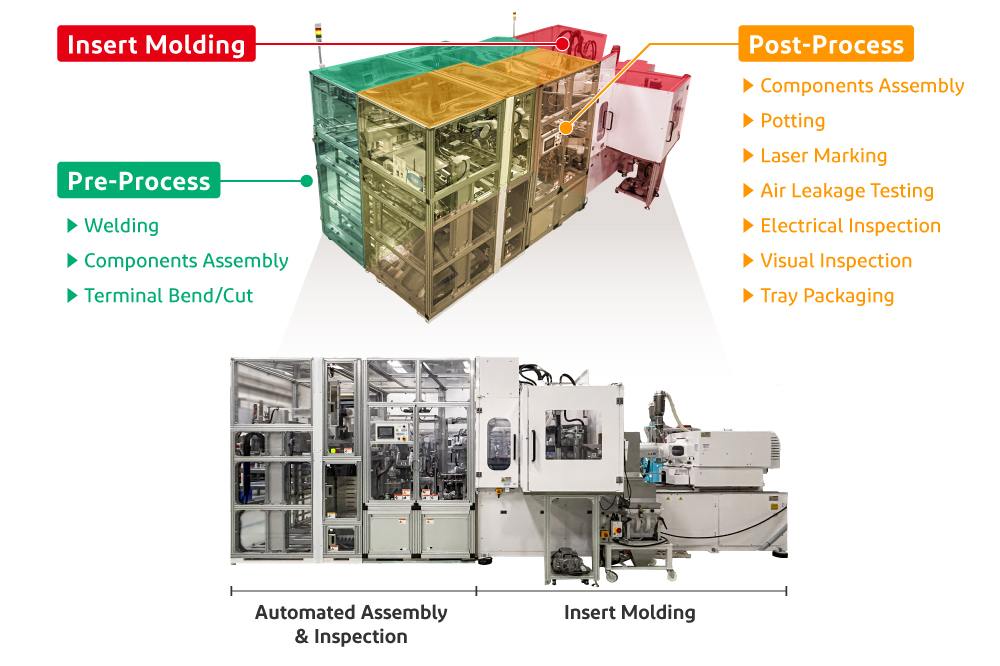